Mit PLM zur papierlosen Fertigung und Model Based Definition

Wie gelingt der Schritt weg von der Zeichnung hin zur papierlosen Fertigung und Model Based Definition? Die Antwort liegt im Product Lifecycle Management.
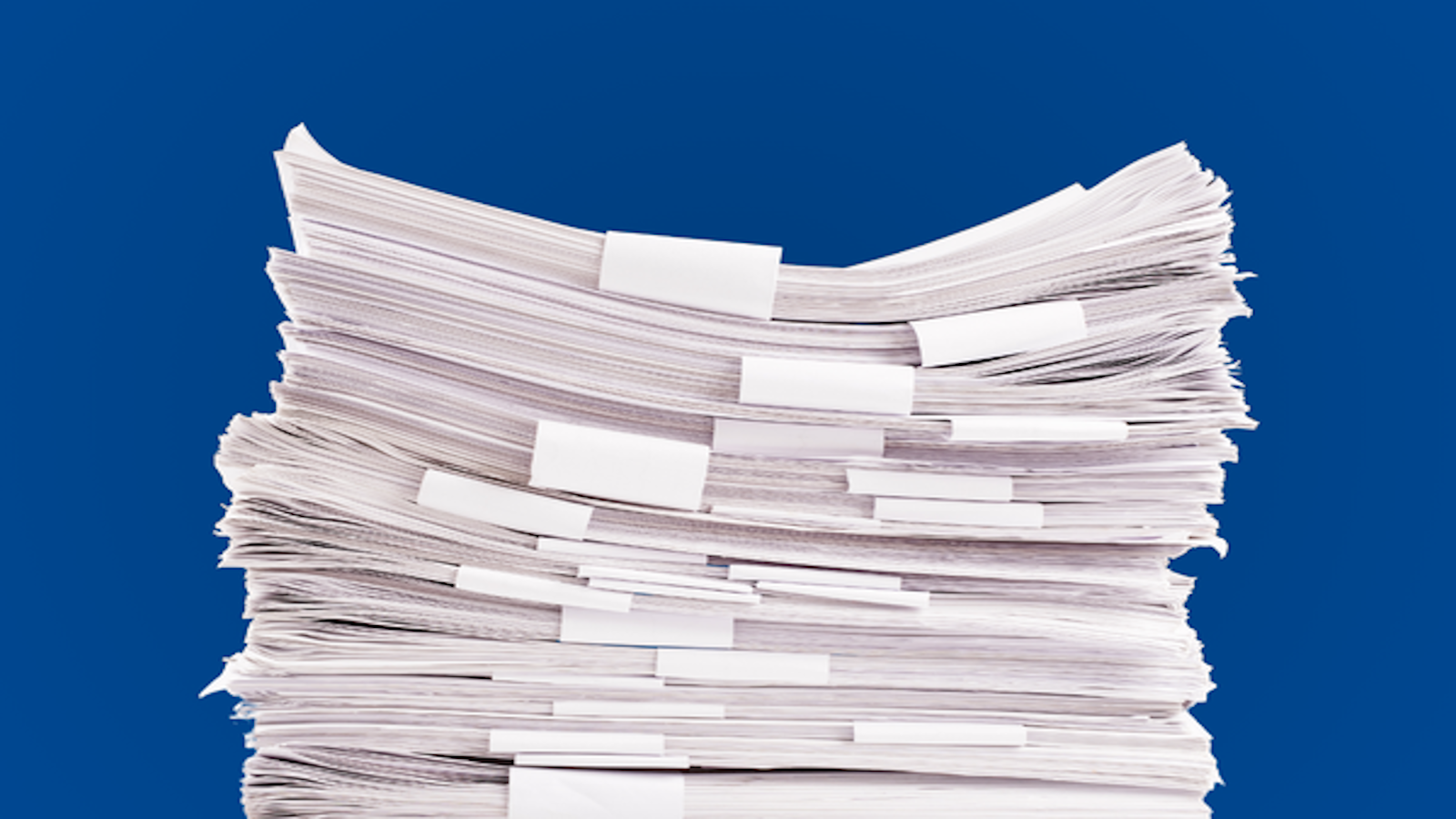
Ölverschmierte Papierstapel, keine Möglichkeit, Fehler unmittelbar an die Konstruktion zurückzumelden und die stete Frage, ob die ausgedruckte Zeichnung überhaupt aktuell ist – Eine beträchtliche Anzahl der mittelständischen Betriebe im deutschen Maschinen- und Anlagenbau setzt noch immer auf ausgedruckte Zeichnungen in der Fertigung. Dabei setzen immer mehr Unternehmen die papierlose Fertigung um oder haben den Prozess bereits angestoßen. Und wenn man schon einmal dabei ist, die Prozesse neu zu denken, ist der Schritt weg von 2D hin zur unternehmensweiten Nutzung von 3D-Modellen gar nicht mehr weit und die Zeichnung somit überflüssig. Ein PLM-System mit intelligenten Funktionen bietet hier die notwendige Unterstützung.
1. Papier ist geduldig – Produktionsprozesse jedoch nicht: Herausforderungen der Papierdokumentation
In die Zeitung von heute wird morgen Fisch gewickelt – Dieses Sprichwort macht auf einen großen Nachteil aufmerksam, der allen auf Papier festgehaltenen Informationen gemein ist: Sie sind vergänglich. Neben der fehlenden Aktualität sind noch weitere Herausforderungen mit der Nutzung von Papierzeichnungen in der Fertigung verbunden. So sehen sich Unternehmen mit steigenden Anforderungen im Bereich der Nachhaltigkeit konfrontiert, beispielsweise durch CO2-Vorschriften. Auch gestaltet sich die Zusammenarbeit im Produktentstehungsprozess immer komplexer, da Entscheidungen zunehmend abteilungsübergreifend getroffen werden müssen, beispielsweise durch die Verwendung mechatronischer Komponenten. Auch besteht kein durchgängiger Informationsfluss und es kommt regelmäßig zu Medienbrüchen, da in der Regel viele nicht miteinander verknüpfte Expertensysteme vorliegen und die Informationen manuell übertragen werden müssen. Dies ist nicht nur äußerst fehleranfällig, sondern bindet auch wertvolle personelle Ressourcen für nicht-wertschöpfende Tätigkeiten.
2. Von der papierlosen Fertigung über PMI bis hin zum Model Based Enterprise
Die Realisierung einer papierlosen Fertigung ist demnach mit vielen Vorteilen verbunden. Hierfür werden die digitalen 2D-Zeichnungen über eine Viewing-Möglichkeit direkt in der Fertigung abgerufen, anstatt sie auszudrucken. Damit gehören ölverschmierte Papierstapel zwar der Vergangenheit an, es muss jedoch weiterhin stets eine 2D-Zeichnung abgeleitet werden. Auch Probleme, wie beispielsweise die Realisierung abteilungsübergreifender Zusammenarbeit, Medienbrüche und die damit verbundene Fehleranfälligkeit, bleiben bestehen. Es lohnt sich also, den Prozess weiter zu denken und die Verwendung von Product Manufacturing Information (PMI) im Unternehmen einzuführen. Hierbei werden fertigungsrelevante, nicht geometrische Informationen an das 3D-Modell angehängt, um sie der Fertigung zu übermitteln. Dies bildet den Grundbaustein für die Praxis der Model Based Definition, also der vollständigen digitalen Definition eines Produktes innerhalb des 3D-Modells, inklusive Geometrie, PMI und Metadaten. Wird dieses angereicherte 3D-Modell nicht nur in den technischen Abteilungen, sondern unternehmensweit und in der Kommunikation mit externen Lieferanten verwendet, spricht man von einem sogenannten Model Based Enterprise.
3. Maßnahmen auf dem Weg zum Model Based Enterprise
Um ein digitales Produktmodell im Unternehmen vollumfänglich nutzbar zu machen, müssen verschiedene Maßnahmen ergriffen werden.
Zunächst einmal bedarf es einer lückenlosen Verknüpfung der Kommunikation rund um das Produkt. Die Grundlage hierfür bildet ein PDM/PLM-System. Notifikationen, die automatisch verteilt werden, erhalten den Informations- und Kommunikationsfluss aufrecht. Außerdem muss die Verteilung von Informationen systemisch abgebildet werden.
Eine weitere Grundvoraussetzung ist der unternehmensweite Zugriff auf ein zentrales digitales Produktmodell inklusive Viewing-Funktionalitäten. Dafür sollten sämtliche fertigungsrelevante Informationen innerhalb eines 3D-Modells abgebildet werden. 2D-Zeichnungen werden somit überflüssig. Das dreidimensionale Produktmodell bietet viele Vorteile, da es insbesondere bei hochkomplexen Maschinen ein besseres Produktverständnis schafft und für alle Abteilungen im Unternehmen leichter konsumierbar ist. Ein wichtiger Baustein dabei ist die Erzeugung von 3D-Neutralformaten, da diese besser im gesamten Unternehmen genutzt werden können. Hier ist insbesondere das JT-Format hervorzuheben: Es hat eine geringere Dateigröße als das native CAD-Format und kann sowohl PMIs als auch unterschiedliche Modellansichten mitausliefern. Auch dabei kann das PDM-System, behilflich sein, beispielsweise durch einen Formatserver für die automatische Generierung von neutralen Formaten sowie die Bereitstellung kostenloser Viewing-Möglichkeiten für das gesamte Unternehmen. So bietet beispielsweise die neueste Version der PDM-Lösung EdgePLM COMPACT einen JT-basierten 3D-Viewer.
Damit der Schritt hin zur papierlosen Fertigung und der Arbeit mit dem digitalen, dreidimensionalen Produktmodell im Unternehmen gelingt, muss zudem eine hohe Anwenderakzeptanz bei der Softwarebedienung erreicht werden. Dies gelingt durch geringe Einstiegsbarrieren und die Aussicht auf schlanke Prozesse durch den Wegfall von Zeichnungen.
Abschließend bleibt zu betonen, dass es sich um einen Prozess handelt, welcher unbedingt ganzheitlich gedacht werden muss. Die Anforderungen an das digitale Produktmodell sollten demnach sowohl unternehmensintern und abteilungsübergreifend als auch mit Zulieferern definiert werden.
4. Wann werden Sie papierlos?
Wer die Prozesse in seinem Unternehmen auf eine papierlose Fertigung und Model Based Definition umstellt, wird mit zahlreichen positiven Effekten belohnt. So herrscht durch den digitalen Zugriff mehr Ordnung in der Fertigung und Papierstapel oder ölverschmierte Zeichnungen lassen sich ab sofort vergeblich suchen. Viel weitreichender ist jedoch der Effekt auf die Kommunikation im Unternehmen, da hier Lücken nahtlos geschlossen werden können und durch den abteilungsübergreifenden Zugriff auf die digitalen aktuellen 3D-Daten ein interdisziplinäres Produktverständnis geschaffen wird. Dies resultiert schlussendlich in weniger Rückfragen bei Nacharbeiten und weniger invaliden Änderungsanfragen z. B. aus der Fertigung, da der Gesamtkontext der Produktinformationen viel besser einschätzbar wird. Auch wird so die Aktualität der Daten gewährleistet und Fehler sowie Missverständnisse werden vermieden. Zusammenfassend ist also eine deutliche Zeit- und Kostenersparnis zu erwarten. Offen bleibt also nur noch eine Frage: Wann werden Sie papierlos?

23. November 2023