Simulation in der Fertigungsindustrie – der Blick in die digitale Kristallkugel
Intelligente Simulationslösungen: Sie bewältigen steigende Anforderungen wie Nachhaltigkeit und Energieeffizienz und optimieren den gesamten Produktentstehungsprozess.
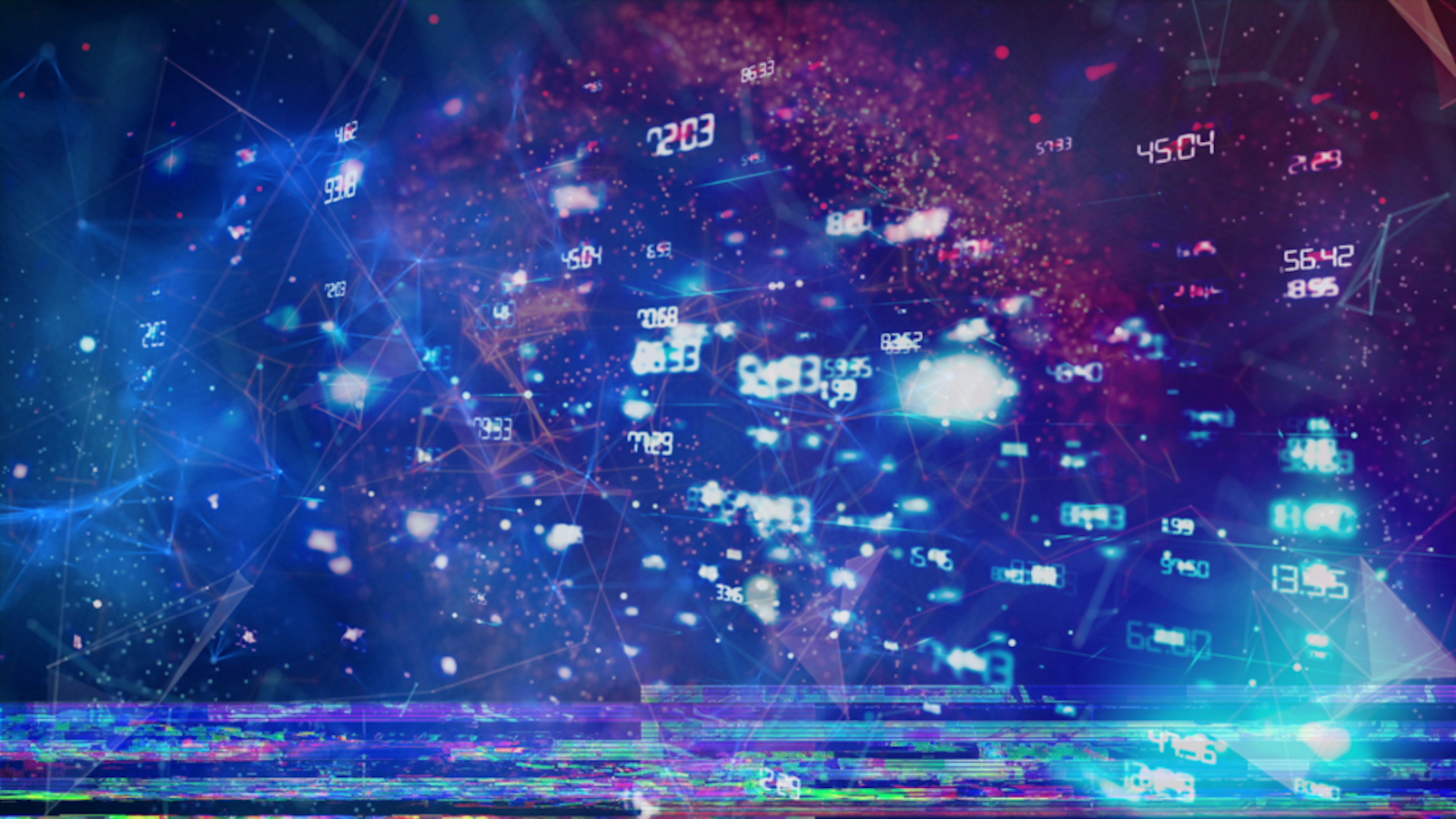
Immer komplexere Produkte, eine gestiegene Nachfrage an kundenspezifischen Anpassungen oder Themen wie Nachhaltigkeit und Energieeffizienz sind nur einige der wachsenden Anforderungen, mit denen sich Hersteller in der heutigen Zeit konfrontiert sehen. Wer wünscht sich da nicht eine Kristallkugel, in die man über den gesamten Produktentstehungsprozess hinweg einen Blick werfen könnte, um böse Überraschungen und kostspielige Fehler zu vermeiden? Hier kommen in der digitalen Fertigungsindustrie intelligente Simulationslösungen zum Einsatz und sparen bares Geld und Zeit.
Visualisierung von Produktplanung bis Fertigung
In der Produktentwicklung wird Simulation eingesetzt, um zu überprüfen, ob eine Konstruktion wie geplant funktioniert und somit die Anzahl an Tests, physischer Prototypen und nachträglicher Änderungen drastisch zu reduzieren. Dabei wird sie zusammen mit der Visualisierung über den gesamten Produktentstehungsprozess genutzt, von Produktplanung und Design über die Entwicklung und Konstruktion bis hin zu Bereichen wie dem Vertrieb, der Produktion, der Inbetriebnahme oder der Entsorgung.
Auch bei der Planung von Fertigungsanlagen oder Fabriken wird auf Simulation zurückgegriffen, um eine reibungslose Produktion sicherzustellen und kostspielige Korrekturen zu vermeiden. Dabei finden unterschiedliche Technologien wie die Finite Element Methode (FEM) in der Konstruktion, die Ablaufsimulation in der Produktion, die Visualisierung bei Virtueller Inbetriebnahme und AR- und VR-Anwendungen im Service Verwendung.
Wettbewerbsfähig bleiben dank Simulation
Simulation bietet demnach einen echten Wettbewerbsvorteil: Sie beschleunigt die Produktentwicklung und ermöglicht es so, kostengünstigere und zuverlässigere Produkte auf den Markt zu bringen. Insbesondere kleine und mittelständische Unternehmen sind stets gefordert, mit diesem Wettbewerb mitzuhalten – auch hier liegt der Schlüssel in der Digitalisierung.
Gemäß einer Befragung des Verband Deutscher Maschinen- und Anlagenbau (VDMA), arbeiteten im Jahr 2020 knapp 30 Prozent der deutschen Maschinenbauunternehmen mit einer Simulationslösung. Am häufigsten kamen diese in der Konstruktion und Entwicklung zum Einsatz. Jedoch war ein wachsender Anteil von Systemen zur Virtuellen Inbetriebnahme zu verzeichnen. Hierbei dient die Simulation zur Erstellung eines Digitalen Zwillings, mit dessen Hilfe Produkte bereits lange vor der eigentlichen Produktion simuliert und optimiert werden können. Anschließend fließt der Digitale Zwilling auch in die Planung der Fertigungsanlagen ein, die ebenfalls virtuell geplant, simuliert und sogar in Betrieb genommen werden kann.
Simulation spart kostbare Zeit
Zeitersparnis ist also einer der grundlegenden Vorteile von Simulation. Ohne sie könnte es beispielsweise vorkommen, dass der Konstrukteur erst nach der Fertigung von Problemen seines Produktes erfährt, die schon weitaus früher und bevor ein Großteil der Kosten feststand, hätten gelöst werden können. Intelligente Softwarelösungen helfen, solche kostspieligen Fehler zu vermeiden. So beispielsweise Berechnungstools für Finite-Elemente-Analysen (FEM) für CAD-Systeme, wie Solid Edge Simulation von Siemens. Damit können Konstrukteure eigene Simulationen durchführen.
Neben reduzierten Kosten für ausgelagerte Berechnungen und mehr Berechnungen in kürzerer Zeit können so die Anzahl teurer realer Prototypen, Material- sowie Testkosten reduziert werden. Weitere nützliche Funktionen bieten Programme wie Simcenter FLOEFD und Simcenter Flomaster für Solid Edge. Ersteres ermöglicht es, die numerische Strömungsmechanik (CFD) bzw. die Simulation schon im frühen Stadium des Konstruktionsprozesses durchzuführen. Mit dem zweiten können schnelle, flexible und genaue Modellierungen von Thermofluidsystemen, einschließlich Strömungsgeschwindigkeit, Temperatur und Druckverlust erstellt werden.
Weg von der Verifikation – hin zur Vorhersage
Es ist bereits deutlich geworden, dass die Zukunft von Simulationspraktiken in einem Ansatz im Bereich des Digitalen Zwillings liegt. So gelangt man von einem ursprünglich verifikationszentrierten Prozess hin zu einem prädiktiven Ansatz, mit dem die Leistung über sämtliche kritische Attribute hinweg früher und während des gesamten Produktlebenszyklus prognostiziert werden kann – ähnlich wie mit der besagten Kristallkugel. Die Rede ist dann von Predictive Engineering Analytics (PEA). Ein Ansatz im Entwicklungsprozess, der auf Basis virtueller Modelle des echten und genutzten Produkts Anforderungen verifiziert und validiert. Auch hierfür bedarf es einer intelligenten Softwarelösung, die den Aufbau eines Digitalen Zwillings unterstützt, wie beispielsweise Simcenter von Siemens. Die Software ermöglicht es, Berechnungsspezialisten rechtzeitig in den Produktentstehungsprozess einzubinden und in jeder Phase der Produktentwicklung zu simulieren und testen. Dafür bietet sie effiziente multidisziplinäre Simulationsprozesse, gepaart leistungsstarken Software- und Hardware-Lösungen für die abschließende Absicherung in einem möglichst realitätsnahen, physikalischen Test und somit eine einzigartige Lösung zur Kombination von Systemsimulation, 3D-CAE und Tests.
Sie sind an einer ganzheitlichen intelligenten Simulationslösung für Ihr Unternehmen interessiert? Sprechen Sie uns an!
25. November 2023